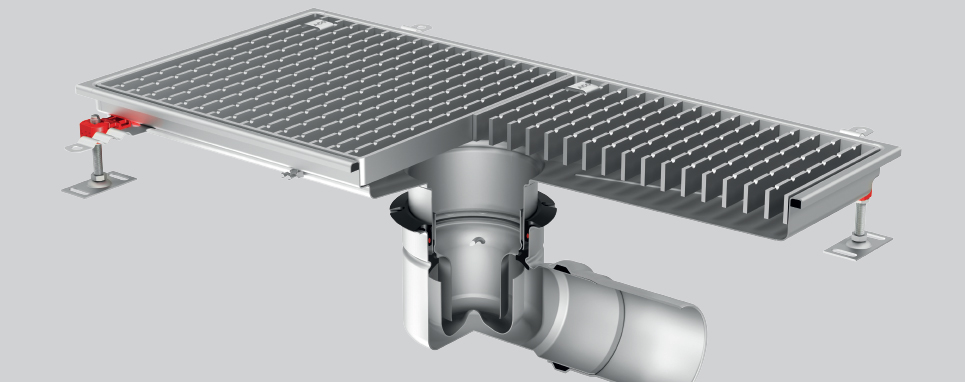
Optimising hygienic performance with drainage design I
In our latest HygieneFirst Showcase article our Key Account Manager, Brett Ira, highlights some of the key factors to consider when specifying hygienic drainage for food processing environments.
Picture gallery
Hygienically designed drainage is critical for any food related business. Recent research underlines that poor hygiene in foodservice and food manufacturing environments can be caused as a direct result of bacteria that’s present in a processing facility’s drainage. A hygienically engineered drainage system will minimise the risk of bacterial contamination and prevent cross contamination throughout a food processing facility.
Importantly, a well designed, high quality drainage system – one which is made from fully pickle passivated stainless steel - will also keep employees safe by helping to prevent slip related workplace injuries and minimise operational costs by ensuring cleaning is a quick, easy process and ongoing maintenance requirements are small.
So what are the key design features to look for when evaluating different drainage systems? As an absolute minimum, we recommend the following:
1. The drainage system is designed in accordance with the best practice hygienic design principles specified by the European Hygienic Engineering & Design Group (EHEDG). This means, for example, that corners such be rounded with a minimum radii of 3mm, welds must be continuous and not be made on corners or overlapped, and the surface of the drainage needs to be smooth with a roughness factor of 0.3 to 0.5 micro-metres.
2. The drainage is made from stainless steel of Grade 304, 316 or higher. When it comes to food safety, the only real option when specifying a drainage solution is one constructed from stainless steel. Stainless steel is easier to clean and to keep clean than systems made from other materials such as plastic or iron. Consider operating conditions such as acidity and temperature as well as the cleaning methodology you want to adopt when deciding which grade of stainless steel to use.
3. Your stainless steel drainage system should be fully pickle passivated to minimise corrosion and pitting. This is a key recommendation of EHEDG and fabricators that don’t fully pickle passivate their products run the risk of failing to meet longer term durability requirements as well as compromising hygiene.