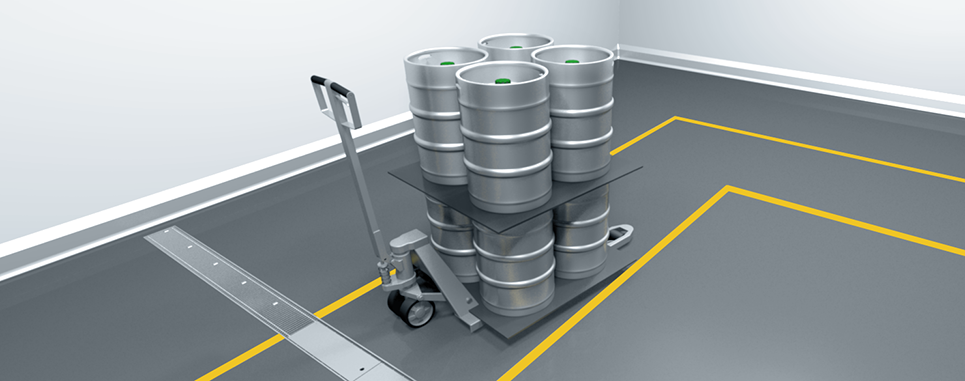
Floor-drainage connection: What the latest research tells us
Reflecting its commitment to putting HygieneFirst, ACO joined forces with leading flooring manufacturer Sika to conduct research into floor-drainage connections and the implications for system specification. Here Jakub Konopac of ACO Industrial Drainage gives an overview of the three-year research project and its key findings.Picture gallery
Why is this research important?
The challenging environments present in today’s food and drink manufacturing facilities require the ongoing development of new hygienic resin flooring solutions and advanced hygienically designed drainage systems. Like other elements within a manufacturing facility, the flooring and drainage systems used affect each other’s performance. Even when flooring and drainage systems are performing well, failure often occurs in the connection between the two. Common failures including cracks, elevation of floor plate edges and delamination often occur because of specification errors such as failing to consider the chemicals that will be used in the manufacturing environment or choosing the incorrect type of drainage. Not only common failures, but also risks associated with running conditions have to be considered during correct specification. Heavy and frequent traffic and thermal exposure play a significant factor affecting the floor-drainage functionality lifetime. This all must be taken into consideration.
Failures in the floor-drain connection, lead to costly downtime and critically, can compromise hygiene but until now no formal research has been conducted to identify the compatibility of common floor-drain connections and to develop best practice specification guidelines. This research was conducted to address this issue so we could provide clear, scientific, evidence-based guidance for factory operators.
How was the research conducted?
The testing itself took place over a period of three years. It involved testing the performance of different drainage edge types with a variety of flooring types. Research was conducted into the three main exposure scenarios that are most relevant to food and drink processing operations: Mechanical exposure in areas experiencing heavy traffic from fork-lifts and pallet trucks; thermal exposure caused by the use of hot water in processing and when cleaning using jet washers, and shrinkage of concrete floor structure which is commonly seen on the top of concrete, screed or resin flooring materials.
Proper testing equipment was selected or developed specifically for each scenario to ensure we could deliver high levels of accuracy and requirements including aesthetics, hygiene, cleanability and ease of installation were factored into the design of the floor-drainage connections being tested.
At ACO, we developed a new rig for the purposes of mechanical exposure testing. The rig enabled us to evaluate the performance of different elements of the floor-drainage connection when exposed to loads generated by vehicular machinery and handling technology commonly used in food and drink manufacturing facilities. We have also built a thermal exposure testing rig to conduct tests according to EN 1253 specification and the Institute Tazus in Brno in the Czech Republic provided us with a testing rig that enabled us to simulate concrete shrinkage.
Two types of standard edge drainage profile and two types of flooring – Polyurethane (Sikafloor-326 + ColorQuartz + SR-169 PUR elastic and self-levelling compound with sand surface) and hybrid (Sikafloor-21 PurCem cement screed modified polyurethane) – were used in tests.
What were the key findings?
Preliminary findings show that there are better outcomes when a certain type of drainage profile is specified with a specific type of flooring for a particular type of application. For example, in typical warehouse applications with a thermal load of no more than 25°C, standard edge drainage profiles connected directly to the flooring perform best. In contrast, in applications where traffic loads of up to 5 tons are present and thermal loads are above 40°C, drainage with L-profile edge proves to be the better performer, being resistant to both the thermal and dynamic shock present.
What are the implications for food and beverage manufacturers?
The findings of our research clearly identify the best floor-drainage connections for a range of manufacturing environments. This information has enabled ACO and Sika to develop clear specification guidance and that means food and drink manufacturers will be able to maximise the durability and hygienic performance of floor-drainage connections in their facilities, both factors which are critical to business continuity and ultimately to protecting public health.